Underrated Ideas Of Tips About What Are The Rules For Wire Splices

How To Splice 4 Gauge Wire
Decoding Wire Splices
1. Why Wire Splices Matter
Okay, let's talk about wire splices. Sounds thrilling, right? Maybe not as exciting as a superhero movie, but trust me, knowing the rules can save you from a shocking experience (literally!). A wire splice, at its core, is just joining two or more wires together to create a continuous electrical circuit. Mess it up, and you're looking at potential electrical hazards, flickering lights, or appliances that refuse to cooperate. Think of it as the unsung hero of your electrical system; when done right, you won't even notice it. But when done wrong... prepare for some electrifying trouble!
Why can't you just twist the wires together and hope for the best? Well, electricity is a finicky thing. A loose or poorly made splice creates resistance, which generates heat. Heat, in turn, can melt insulation, cause short circuits, and even start a fire. Plus, a shoddy splice is like a weak link in a chain the whole circuit's reliability suffers. So, taking the time to learn the right way to splice wires is absolutely crucial for both safety and functionality.
Think of your home's electrical wiring as the veins and arteries of a living organism. Just as a blocked artery can cause serious health problems, a poorly executed wire splice can lead to all sorts of electrical woes. From power outages to potential fire hazards, the consequences can be significant. By understanding and adhering to the rules for wire splices, you're essentially ensuring the healthy flow of electricity throughout your home, protecting your property and loved ones from harm.
Furthermore, improper wire splices can also lead to increased energy consumption. When connections are loose or corroded, they create resistance, forcing your electrical system to work harder to deliver the necessary power. This not only increases your energy bills but also puts unnecessary strain on your appliances and electrical components, potentially shortening their lifespan. So, investing a little time in learning the proper splicing techniques can save you money in the long run.
Common Wire Splices And Joints PDF
The Cardinal Rules
2. Common Splicing Sins
Alright, let's dive into what NOT to do when splicing wires. First off, never, ever skip using wire connectors (wire nuts, Wago connectors, etc.). Taping bare wires together is a recipe for disaster. Think of wire connectors as tiny, insulated fortresses protecting your splice from the dangers of arcing and shorts. They provide a secure, insulated connection that's far superior to just twisting and taping.
Another big no-no is mixing wire types. Copper and aluminum wiring are like oil and water — they don't play well together. When these metals come into contact, they create a corrosive reaction that can lead to loose connections and, you guessed it, potential fire hazards. Always use the correct type of wire for the circuit and, if you absolutely must join copper and aluminum, use a specialized connector designed for that purpose.
Ignoring wire gauge is another common mistake. Using a wire that's too thin for the circuit's amperage is like trying to force a river through a garden hose. The wire will overheat, potentially melting the insulation and causing a fire. Always check the circuit's amperage rating and use a wire gauge that's appropriate for the load. When in doubt, err on the side of caution and use a slightly thicker wire.
Also, don't overload wire connectors! Each connector is designed for a specific number and size of wires. Cramming too many wires into a single connector can lead to loose connections and potential hazards. If you need to join more wires than a connector can handle, use multiple connectors or a junction box to distribute the connections properly. Think of it as avoiding overcrowding a bus — everyone (and every wire) needs enough space to stay safe and comfortable.
:max_bytes(150000):strip_icc()/how-to-splice-electrical-wire-1821560_07_wire_connection_1432-a1ee3a6ac9574de7bfbae6cc58072fa5.jpg?strip=all)
The Right Way to Splice
3. Mastering the Art of the Splice
Okay, now for the good stuff: how to actually splice wires correctly. First things first, always turn off the power to the circuit you're working on! This might seem obvious, but it's the most important step. Double-check with a non-contact voltage tester to be absolutely sure the power is off before you even think about touching the wires. Safety first, always!
Next, strip the insulation from the ends of the wires, exposing just enough bare wire to make a solid connection within the wire connector. Use a wire stripper tool to avoid nicking or damaging the wire. A clean strip is crucial for a good connection. Make sure not to strip off too much insulation, you want the connector to properly cover the uninsulated parts.
Now, carefully twist the stripped ends of the wires together. Some wire connectors require you to pre-twist the wires, while others don't. Follow the manufacturer's instructions for the specific connector you're using. A good twist ensures that the wires are securely connected before you even put on the connector. Think of it like shaking hands with electricity — a firm grip is key.
Finally, screw on the wire connector, twisting it clockwise until it's snug. Give it a gentle tug to make sure the wires are securely held in place. The connector should completely cover the exposed wires, providing a secure and insulated connection. Wrap the connection with electrical tape as an added layer of safety, making sure to overlap each layer of tape. Now, you've got a safe and reliable wire splice! Repeat this step for all wires you are connecting.
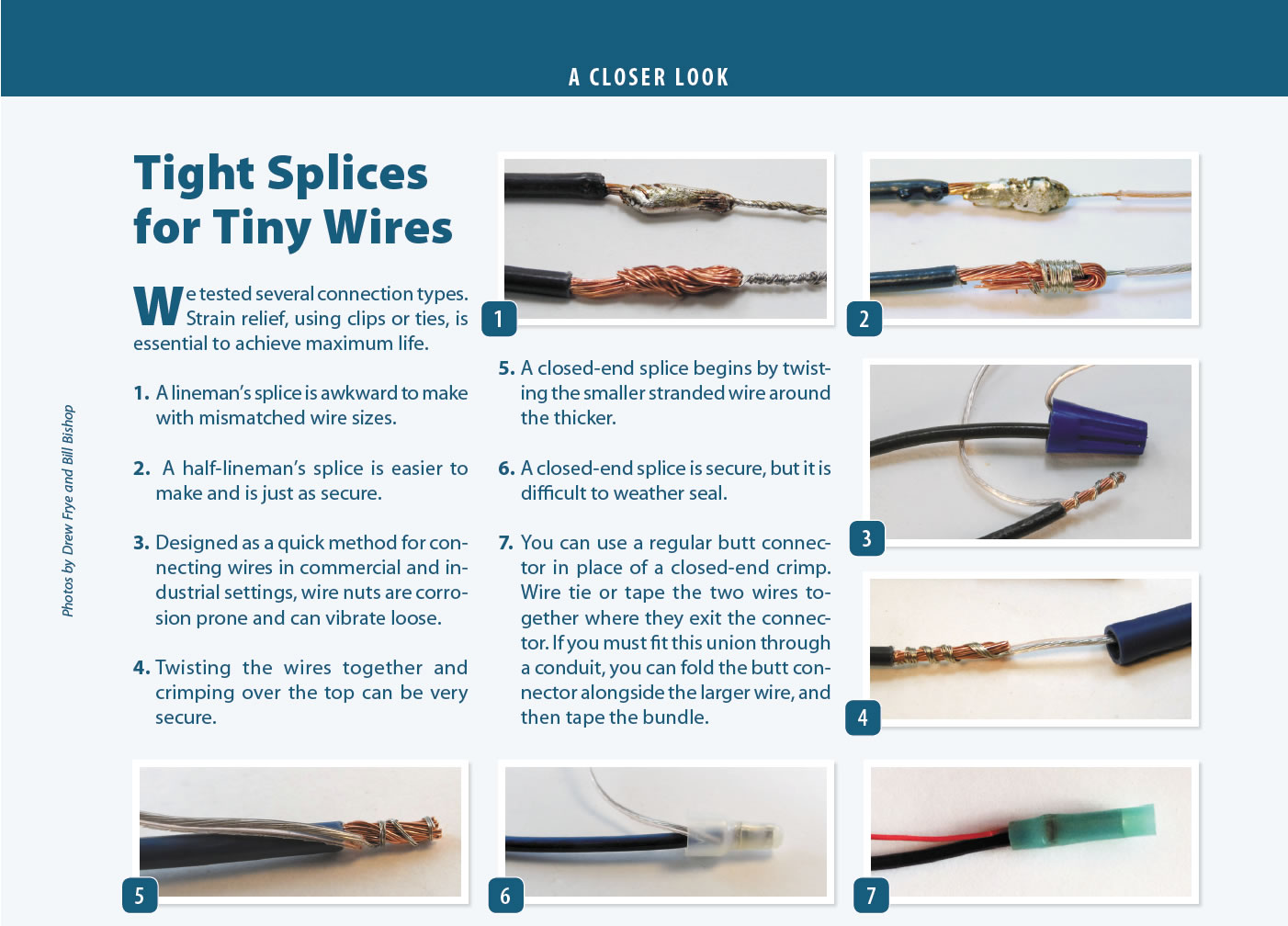
Should You Twist Wires Before Wire Nut IOT Wiring Diagram
Choosing the Right Connector
4. Connector Considerations
Not all wire connectors are created equal. Wire nuts are a classic choice, great for general-purpose splicing. They come in different sizes for different wire gauges and numbers of wires. Wago connectors are a newer option, offering tool-free connections and easy reusability. They're perfect for situations where you might need to make changes or additions to the circuit later on.
For joining solid and stranded wires, lever-style connectors are often the best choice. They provide a secure and reliable connection between these different wire types. And if you're working with aluminum wiring, be sure to use connectors specifically designed for aluminum to prevent corrosion and ensure a safe connection. Remember, using the right tool for the job is just as important in electrical work as it is in any other trade.
Consider the environment where the splice will be located. If it's in a damp or wet location, use waterproof connectors to protect the connection from moisture. Corrosion can quickly degrade a splice, leading to electrical problems. Also, think about the accessibility of the splice. If it's in a hard-to-reach area, choose a connector that's easy to install and maintain.
Don't skimp on quality when it comes to wire connectors. Cheap connectors are often poorly made and can fail prematurely, leading to electrical hazards. Invest in reputable brands and look for connectors that are UL-listed, meaning they've been tested and certified for safety. A few extra dollars spent on quality connectors can provide peace of mind and prevent costly problems down the road. Think of it as investing in the foundation of your electrical system strong connections are essential for long-term reliability.
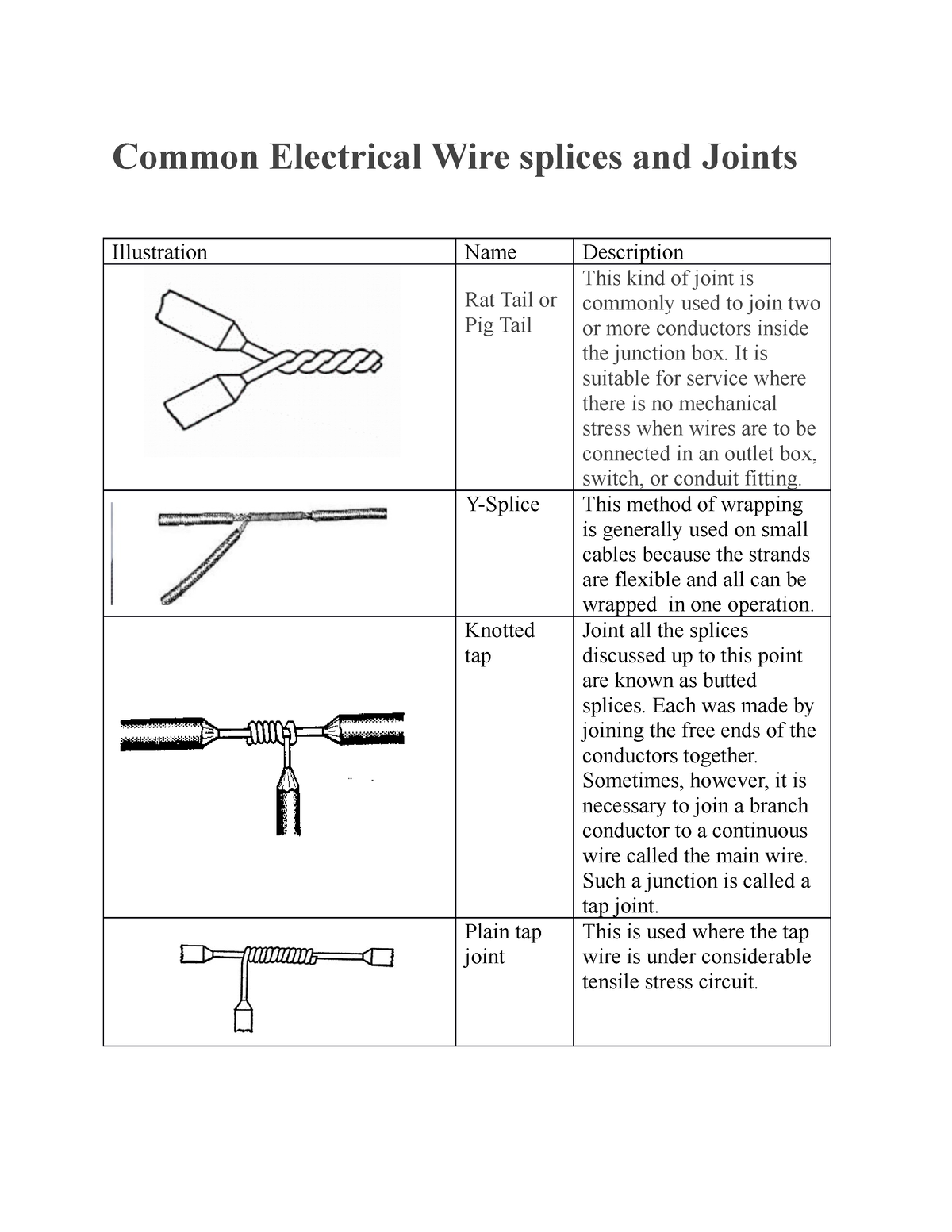
Common Electrical Wire Splices And Joints
Safety First
5. Prioritizing Protection
We've mentioned it before, but it bears repeating: safety is paramount when working with electricity. Always turn off the power to the circuit before splicing wires. Use a non-contact voltage tester to verify that the power is off. Wear safety glasses to protect your eyes from debris. And if you're not comfortable working with electricity, don't hesitate to call a qualified electrician. It's better to be safe than sorry, especially when it comes to electricity.
Never work on electrical projects when you're tired or distracted. Electrical work requires focus and attention to detail. A moment of carelessness can have serious consequences. Also, be sure to have a fire extinguisher nearby in case of an emergency. And if you smell burning plastic or see sparks, turn off the power immediately and investigate the source of the problem.
Regularly inspect your electrical system for signs of damage or wear. Look for frayed wires, cracked insulation, and loose connections. Address any problems promptly to prevent them from escalating into more serious hazards. A little preventative maintenance can go a long way in ensuring the safety and reliability of your electrical system.
Consider investing in arc-fault circuit interrupters (AFCIs) for your home. AFCIs detect dangerous arc faults, which are a common cause of electrical fires. They can provide an extra layer of protection beyond traditional circuit breakers. By taking these safety precautions, you can help protect your home and loved ones from the dangers of electricity.
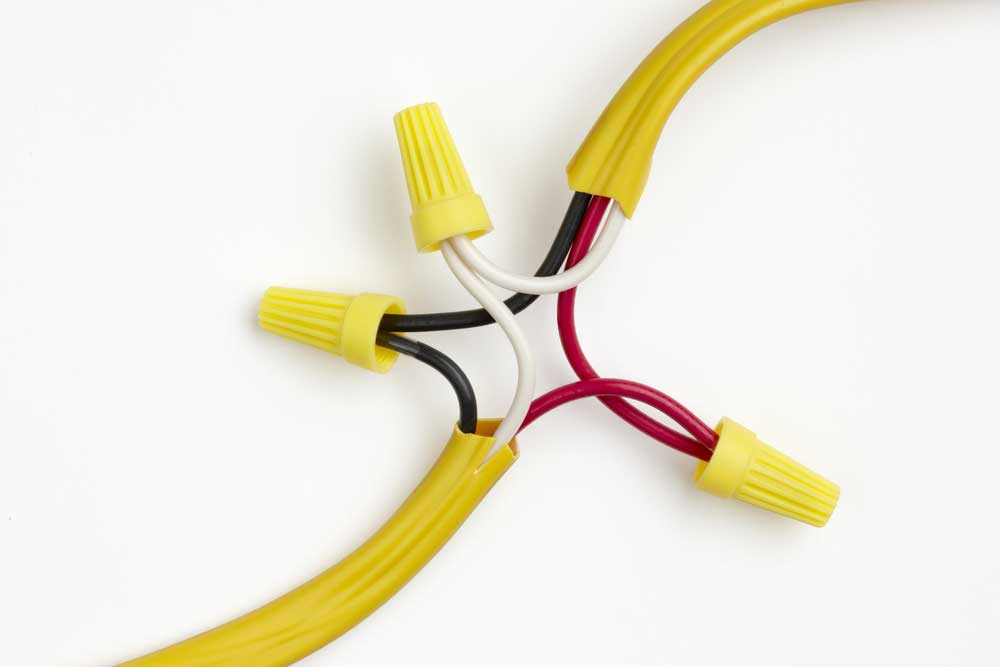
FAQ
6. Q
A: Absolutely, but you'll need to use waterproof connectors and enclosures to protect the splice from the elements. Moisture can wreak havoc on electrical connections, so it's crucial to use the right materials to keep everything dry and safe. Think of it as dressing appropriately for the weather — waterproof gear is essential for outdoor electrical work.
7. Q
A: The golden rule is to use a wire connector that's rated for the different wire gauges you're joining. Some connectors are specifically designed for this purpose. Also, make sure the connector provides a secure and reliable connection for both wire sizes. Don't try to force a small wire into a connector designed for larger wires — that's a recipe for a loose connection and potential problems.
8. Q
A: It's a good idea to visually inspect your wire splices at least once a year, or more frequently if you suspect a problem. Look for signs of corrosion, loose connections, or damaged insulation. If you find anything suspicious, turn off the power and investigate further. Regular check-ups can help you catch problems early and prevent them from escalating into more serious hazards. Think of it as a yearly physical for your electrical system — preventative care is key.